Description
I. MAIN TECHNICAL DATA OF DK7740SF:
ITEM |
UNIT |
DESCRIPTION |
WEDM Guide Rail |
- |
Precision LM Guide |
REMOTE |
- |
CNC REMOTE |
DIGITAL DISPLAY |
- |
With motorised |
Control System |
- |
AutoCut Operating System: Win7/Win10 Graph display simulation |
Machining Axis Qty. |
- |
4-axis Machining |
Work Table Size |
mm |
510*790 |
Max. Loading Weight |
Kg |
600KG |
XY Stroke Size |
mm |
400*500 |
Z-axis Stroke Size |
mm |
300 |
Max.Cutting Thickness |
mm |
300 |
Max. Taper Angles |
- |
+-60 |
Max.Cutting Slope/Thickness |
0/mm |
+-60/80 |
Max.Cutting Speed |
mm2/h |
12000 (200mm2/min) |
Machining Precision |
mm |
Cut accuracy: ≤±0.005mm Straight cutting, ≤±0.012mm |
Surface Finish |
um |
Ra≤0.8-2.5μm (multiple and single path cutting) |
Max.Processing Current |
A |
8 |
Diameter of electrode wire |
mm |
Ф0.18 |
Wire Diameter |
mm |
Ф0.10~Ф0.22 |
Filtration |
mm |
Changeable filter (0.005mm) |
Working Liquid Type |
- |
Water based solution Saponification solution |
Working Liquid Tank Capacity |
liter |
120 |
Working Power |
- |
380-440V AC, 50Hz |
WEDM Consumption Power |
kva |
2.0 |
Wire Shelf |
- |
Adjustable |
Wire Control |
- |
Frequency converter speed regulation |
Input Mode |
- |
Keyboard, U-disk, Network,etc |
Digital Display |
- |
21.5”LCD Display With motorised, |
Power Supply & Control System |
- |
Vertical Control Cabinet |
Minimum Feeding |
mm |
0.001 mm |
Programmee Code |
- |
ISO Code; 3B Language; AUTOCAD/CAM; DXF format file; |
Pulse Width (14 Grades Adjustable) (μs) |
μs |
5-120 |
Adjustable Pulse Interval |
μs |
4-15 |
Machine Size |
mm |
1700MM*1280MM*2100MM |
Machine Weight |
kg |
2600kg |
Packing Size |
mm |
WEDM: 1800*1500*2400 Cabinet: 800*800*1000 |
Packing Weight |
kg |
WEDM: 2600kg Cabinet: 100kg |
Main Functions |
Graphic coordinate transformation, zooming, rotation, graphic tracking display, linear arc interpolation, taper processing, up and down different surface processing, broken wire, short circuit processing, power failure memory, automatic stop after processing, automatic end face, automatic center, reverse processing, menu technology and automatic programming, multiple cutting functions, etc |
II . THE TECHNICAL ADVANTAGE OF DK7740SF:
1). The WEDM is composed of main machine, electrical control system, software part and cooling filter system. The equipment is used for the discharge machining of various complex dies and parts, for the machining of various non-ferrous metals, tool steels, alloy steels and other materials. The main machine of the equipment has high geometric accuracy and position accuracy, and has enough static, dynamic and thermal stiffness and accuracy. The equipment has the functions of taper cutting, variable taper and irregular meshing cutting;
2). The WEDM is composed of main machine, electrical control system, software part and cooling filter system. The main machine is mainly composed of fuselage, column, wire frame, workbench, etc. the structure of the machine tool is compact and the design is reasonable. It has five axes of X, y, u, V and Z, among which the four axes of X, y, u and V are linked and driven by constant current. The vertical cabinet of electrical cabinet is made of cold-rolled steel plate with electrostatic spray molding. The interior of the cabinet is equipped with computer and control software, high-frequency control module, driver, frequency converter, fan, etc. The cooling system includes a water tank, a cooling pump and a filter screen;
3). All castings are cast by resin sand process, natural aging for a long time,
secondary tempering, complete elimination of internal stress, improving the rigidity and accuracy retention of castings, increasing the rigidity of machine tools and reducing the deformation;
4). The machine tool is equipped with a main power switch; the high-frequency is a low-voltage power supply, which is absolutely safe even when it is turned on for processing; the positive terminal is modulated, and the external power supply without voltage residual works normally within 85-120% of the rated voltage range after being turned off, otherwise the power failure protection will be implemented; the power supply of the whole machine has three-phase air switch for over-current protection;
5). Over travel protection for wire transportation, and motor current monitoring through frequency converter to realize motor overheating protection function;
6). Power off and save the processing site, and the computer displays the "power" sound and alarm light Trinity alarm for 10 seconds;
7). All protections that cause the machine tool to stop processing have corresponding indicator lights and fault information code prompts, which is convenient for fault, pseudo fault (caused by improper operation of the user), alarm positioning, adjustment and maintenance;
8). Variable frequency speed regulation of wire conveying motor, stable operation, low noise, low speed molybdenum wire installation, safe and reliable, and wide speed regulation range;
9). The user can save the cutting parameters of different materials, different heights, different speeds and different surface roughness, as well as the electric parameters of straightening and edge colliding, so that the design reduces the requirements of the machine operator's technology, and simplifies and facilitates the operation of the machine;
10). Equipped with an emergency stop button, which can be easily pressed to cut off the power supply in case of an accident;
11). All electrical appliances are in the electric cabinet, which is almost free of water and oil pollution. The probability of safety accidents such as leakage, short circuit and line aging of the machine tool is greatly reduced. The operation safety and equipment safety greatly improve efficiency, processing code, etc. It has the functions of screen displaying figure outline, machining trace, relative coordinate, machining code, machining program, tracking trace, etc;
12). Save the current machining state: if the currently cut workpiece is large, it can be saved at any step of the cutting process, and the cutting can continue at the "stop point" of the last cutting after the next power on;
13). Power off protection: if the whole machine tool is suddenly powered off during the processing, the system will automatically restore the original processing state parameters of the machine tool after power on again;
14). Automatic stop: after the cutting, the water pump and the automatic total stop will be automatically closed;
15). Pre pause: set the pause function in advance before the completion of cutting, which can effectively prevent the occurrence of fillings, broken wires and other phenomena;
16). Angle clearing function: it can effectively eliminate the angle collapse;
17). Automatic center calibration function: as long as the operator selects the requirements to be aligned according to the needs, and automatically moves the CNC axis, the system will automatically take points, participate in the calculation of alignment, and eliminate the human error. Centering can be divided into: inner circle centering, square, rectangle centering, collision edge alignment and centering functions;
18). Monitoring function, with processing dynamic tracking and verification function. In case of abnormal conditions such as broken wire, it can immediately stop the machine and give an alarm. When the cutting is completed, there is an alarm sound to remind the user that the cutting has been completed. There are two alarm modes: alarm sound prompt and control software interface prompt;
19). It has the function of processing interrupted wire shutdown protection and short circuit automatic return;
20). Support the backlash compensation function, which can compensate the screw backlash error of the machine tool, so as to improve the accuracy of the machine tool;
21). It has corner processing function to improve the deviation caused by electrode wire bending;
22). A variety of processing methods can be flexibly combined (continuous, single-stage, forward, reverse, backward and other processing methods).
23). Taper correction calculation: it has the functions of equal taper, variable taper and upper and lower special-shaped cutting, calculates the guide wheel radius, electrode wire diameter, unilateral discharge gap and ellipse error of large taper, and corrects the taper processing parameters to eliminate the theoretical error of taper processing;
24). The graphic format is directly processed by WEDM Process, generating 2D or 3D data of WEDM and processing parts. Support the processing code generated by various WEDM software;
25). When the skip die is cut, the priority of cutting pattern can be selected;
26). It has the function of automatic straightening, after the taper cutting, the molybdenum wire automatically returns to the vertical initial state, which is convenient for use;
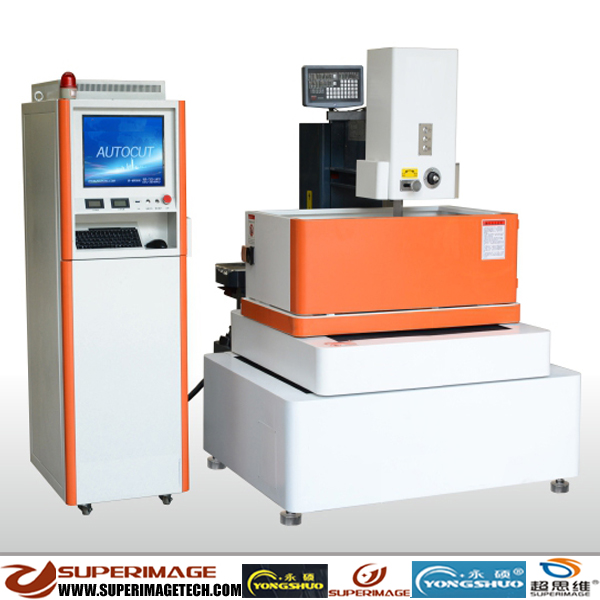
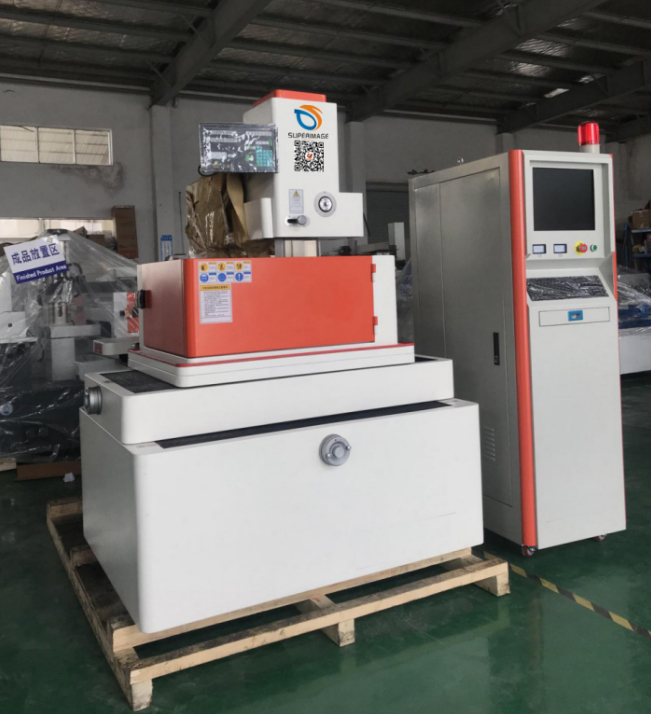